Fiber Optic Communication Systems Agrawal Solution Manual Free Download Facebook
Globally, more than 3.5 billion people are still not connected to the internet . With average data usage per person growing 20 to 30 percent annually , legacy bandwidth-limited technologies have been pushed to their capacity limits. To meet this increased demand for high-capacity, low-cost networks, mobile network operators have upgraded access technologies from 2G and 3G to 4G and beyond, while wireline access networks have moved from DSL and coaxial to fiber to the home. Regardless of the access technology used, to support the increased capacity served in a region, fiber must be brought from the backbone closer to the end user. Facebook Connectivity, in collaboration with a number of partners, has spent the last few years developing an aerial fiber deployment solution that uses a robot designed to safely deploy a specialized fiber-optic cable on medium-voltage (MV) power lines.
This system combines innovations in the fields of robotics and fiber-optic cable design to dramatically lower the cost of deploying fiber by utilizing electrical infrastructure. While there have been tremendous improvements in the strength and size of a fiber strand, as well as the amount of data a strand can carry, there has not yet been a widely applicable solution for reducing the cost of fiber construction. Since the cost of deploying fiber comes almost entirely from construction, this was the area we wanted to address. If successful, we believe this technology will allow fiber to effectively and sustainably be deployed within a few hundred meters of much of the world's population. We expect to see technology trials of this fiber deployment system next year.
We aim for this technology to enable equal construction of fiber in rural and lower-income communities as well as affluent ones, with open access to the fiber, fair and equitable pricing, decreasing prices for capacity as traffic grows, and shared benefits of the fiber network with the electric company.
Facebook has identified NetEquity Networks as the first partner to deploy this new innovative technology and intends to provide NetEquity Networks with a nonexclusive royalty free license to deploy fiber networks using this technology. Facebook does not have a financial stake in NetEquity Networks and will not own or operate fiber networks deployed by them.
The idea
Today, fiber is a critical element to bringing more people online at faster speeds because it has a bandwidth thousands of times greater than that of any other technology. However, the cost and complexity of deploying fiber networks has inhibited large-scale deployment.
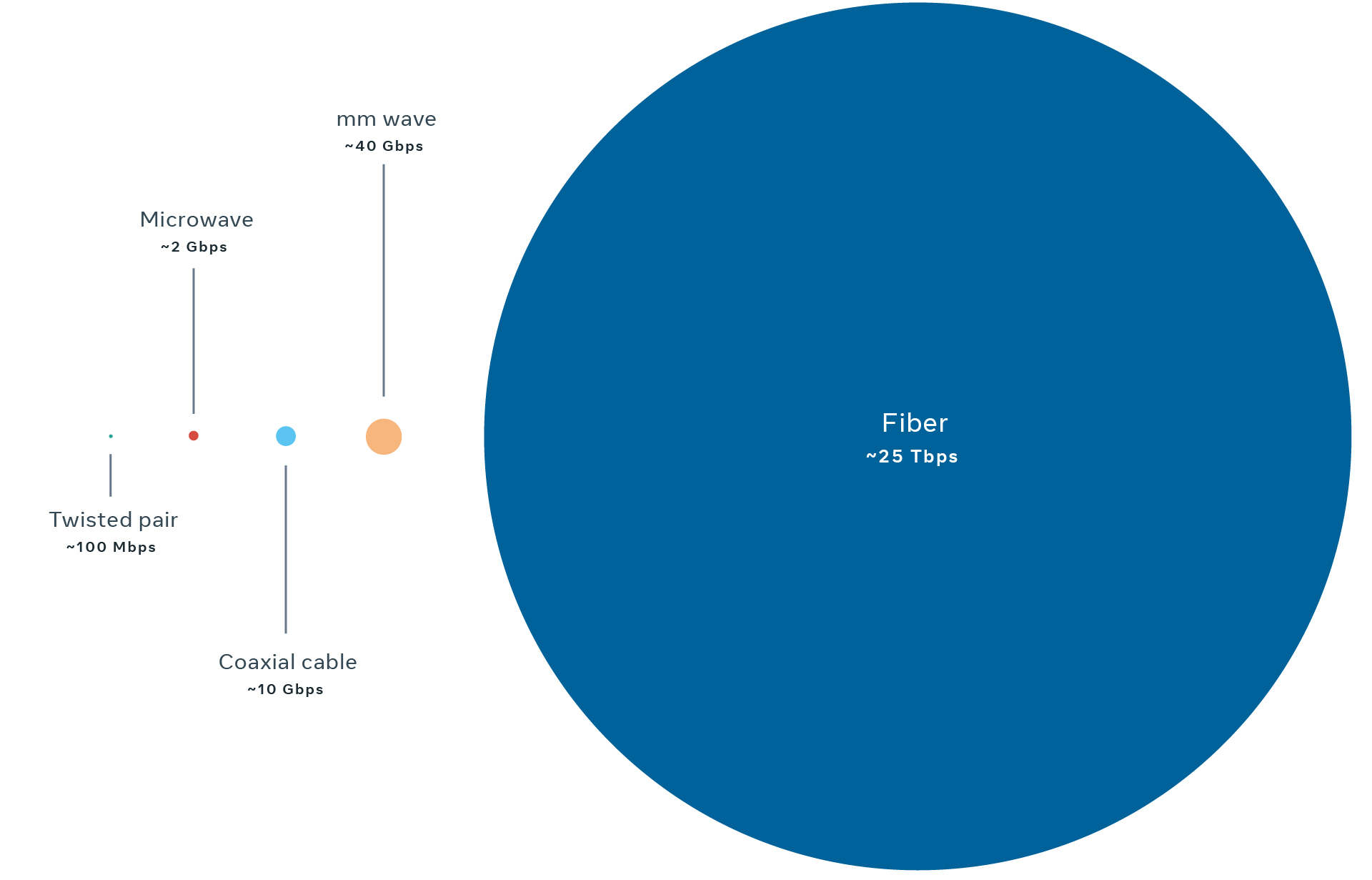
As of 2019, more than 70 percent of the world's population lives more than 10 km from fiber . This has been painfully illustrated during the recent pandemic as communities have had to adapt to near constant usage of the bandwidth-intensive applications required for remote work and schooling.
The idea of utilizing electrical infrastructure first came to us after we saw the ubiquity of electrical grid infrastructure while traveling across rural Africa. The World Bank lists Uganda as having an electrification rate of only ~43 percent as of 2018, yet we can see that the MV grid (shown in yellow) is orders of magnitude more pervasive than the total fiber footprint of the country (shown in red).
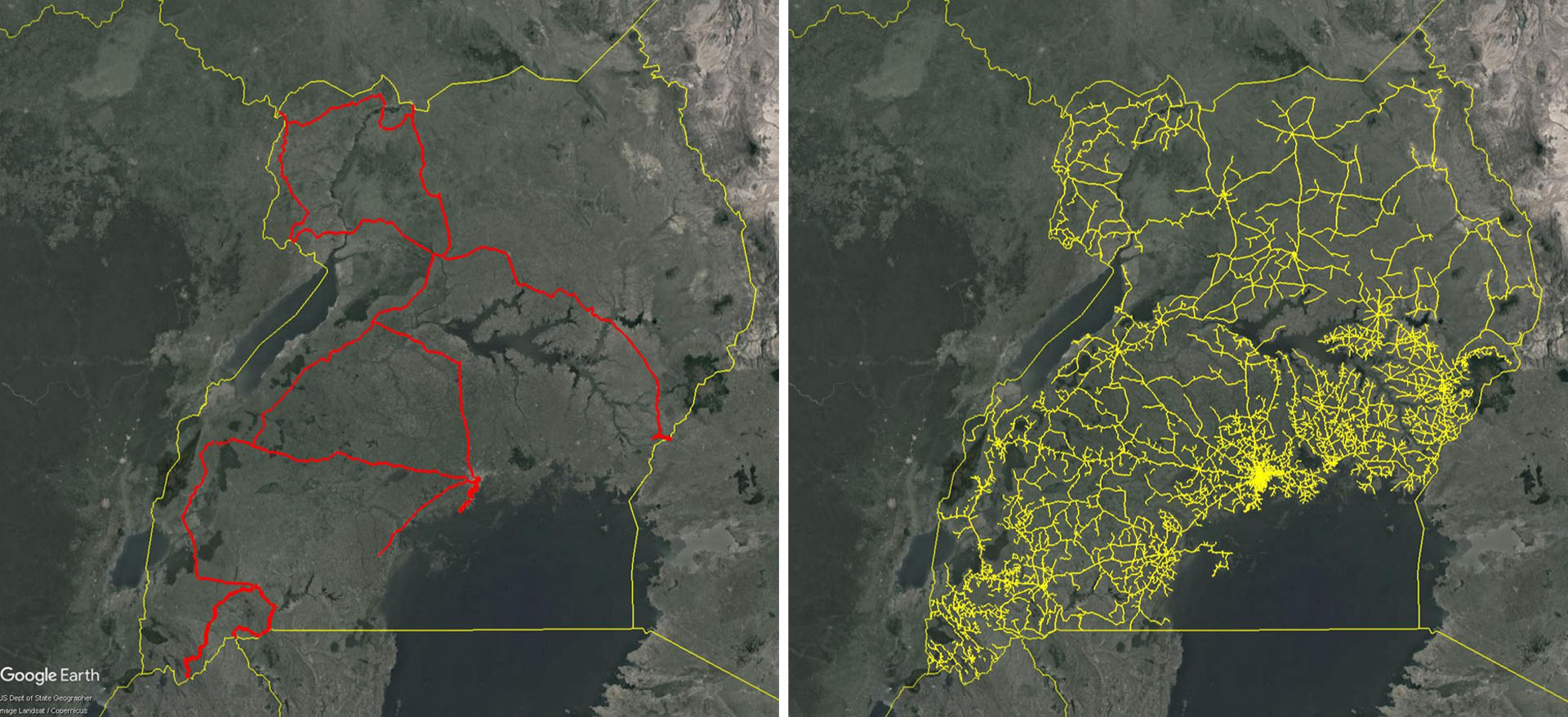
With long transmission lines typically suspended on tall lattice towers, electrical transmission grids serve a function similar to internet backbone, connecting generation sites to substations. From substations, power travels along MV lines into communities for distribution. The electrical grid architecture was designed to cost-effectively distribute power to homes and businesses. We realized that following the same grid with fiber could be an efficient way to build an end-to-end telecommunications network. Because underground construction is significantly more expensive than aerial construction, power infrastructure is almost exclusively aerial outside of city centers and affluent communities. To utilize the electrical grid and lower the cost of fiber deployments, we therefore chose to focus on aerial fiber construction.
When an aerial fiber deployment takes place, existing infrastructure must be prepared to support the new fiber cable attachment, including surveying and analyzing the pole loading, moving existing attachments, adding guy wires, and upgrading poles. This work is collectively referred to as make-ready work, and it represents a sizable portion of aerial construction costs. In the electric utility sector, one operation that doesn't trigger this make-ready work is attaching a splice to repair a broken power-line conductor. Repair splices weigh roughly a pound each, and utilities typically allow a few of these to be added to a line without requiring any make-ready work, since the incremental load is insignificant relative to the weight of the conductor it is attached to. This fact is not relevant to traditional aerial fiber deployment — but it is of great significance to a less common method of fiber-optic installation known as helical wrap or optical attached cable.
Wrapping fiber
Pioneered in the early 1980s, the helical wrap method used a machine to wind a fiber-optic cable around an existing power-line conductor. Since the fiber cable is wound around a supporting conductor, it is not necessary to make a new space on the pole or pull it at a high tension. This obviates the need for expensive, time-consuming make-ready work.
For both aerial high-voltage (HV) and MV power lines, the almost ubiquitous bare overhead conductors rely on clear space around the conductor to prevent arcing and fires. This space also provides a convenient path for a machine to travel. The helical wrapping machine worked by using a simple geared mechanism to lock forward movement along the power-line conductor to a rotating section, which spun a spool of fiber and a counterweight around the conductor. The clearance around the conductor and its strength determined how much fiber could be carried at a time. Forward movement was provided by a gas-powered motor or a person towing the machine with a rope. Crossing obstacles was done manually, with cranes needed to lift the machine past obstacles. Loading and unloading the machine relied on cranes or helicopters. Due to these limitations, the helical wrap approach has primarily been used only for the transmission grid. Since MV lines, unlike transmission lines, run within a few hundred meters of most of the world's population, finding a way to cost effectively wrap fiber on the MV grid could make a significant impact on global connectivity.
But MV conductors are a significantly more challenging environment for a helical wrapping machine. There are approximately 10 times more obstacles for a given distance of MV conductor, so a manual method of crossing obstacles wouldn't be cost-efficient. And to maintain grid uptime, installation needs to be performed while the lines are energized, meaning that human contact needs to be minimized to ensure the safety of line workers. The clearances around MV conductors are also an order of magnitude smaller, which prevents a traditional spool or wrapping machine from carrying a useful amount of cable. Complicating things further, the conductors used for MV power lines are thinner and weaker, limiting the total combined weight of the wrapping machine, fiber cable, and counterweight. Our fiber deployment system is a MV helical wrap solution that addresses these challenges to deliver a 3x to 5x cost reduction in aerial fiber construction.
Developing the system
The size and weight of the fiber cable are the most important factors in making helical wrap cost-effective in the MV space. Fusion splicing to join sections of fiber cable is a slow, expensive process, so there is a minimum continuous length of fiber cable that should be deployed. Since two machines traveling in opposite directions could carry connected back-to-back reels of fiber, the maximum distance between splices is twice the capacity of the wrapping machine. To enable compatibility with the thinnest power-line conductors, we chose a minimum cable capacity per robot of a little more than 1 km.
Although outdoor fiber cables are only a few millimeters larger in diameter than typical indoor cables, the size and weight of a kilometer length of outdoor fiber cable is more than 10x greater.
So why is the diameter of the fiber cable used in traditional fiber construction so large? The primary driver of cable diameter is the number of strands contained in it. A single fiber strand has 53,000 GHz of bandwidth. This would be more than enough bandwidth to meet the capacity needs of an entire region. However, as optical link budgets are limited, insertion loss and splitter losses must be carefully managed, limiting the number of times an optical signal can be split, which in turn limits the number of endpoints that can be fed from a single fiber. Since the cost of construction is significantly higher than that of a fiber strand and the number of customers of a particular fiber route is not often predictable, companies typically overprovision the number of fibers.
However, a fiber network deployed following the MV grid has a big advantage: A fiber cable following a MV feeder will never pass more homes than the electric feeder was designed to serve. This maximum number of homes is determined by the size of the power-line conductor and the transformer feeding it. This is typically a few thousand homes per feeder, but in developing countries it can get as high as 15,000 homes per feeder. Through the use of suitably selected optical components, a wholesale lit service could be offered to serve all of these homes and businesses from a 24-strand fiber cable. These 24 strands are a beneficial strand count, as they enable the use of a single loose tube in place of the four or more typically used in outdoor fiber cables, shrinking the core of the fiber cable.
Beyond all the usual mechanical and environmental stresses an outdoor fiber optic cable must survive, using the MV power line as a support adds a number of additional challenges. The first is the voltage stress. MV conductors can have a voltage as high as 35kV which can cause degradation phenomena such as tracking, partial discharge, and dry band arcing. The power line can also see elevated temperatures far above the melting point of typical fiber-optic jackets, and the stretching of the power line due to thermal changes and wind-induced aeolian vibration can induce strain on the fibers.
To solve these challenges, we brought in veteran cable designer Wayne Kachmar. Developed with a number of partner companies and academic advisors, the resulting design uses G.657 200 micron fibers with a specially tailored aramid configuration and a high-strength, high-temperature, track-resistant polymer jacket to survive the requirements of this application within a small form factor.
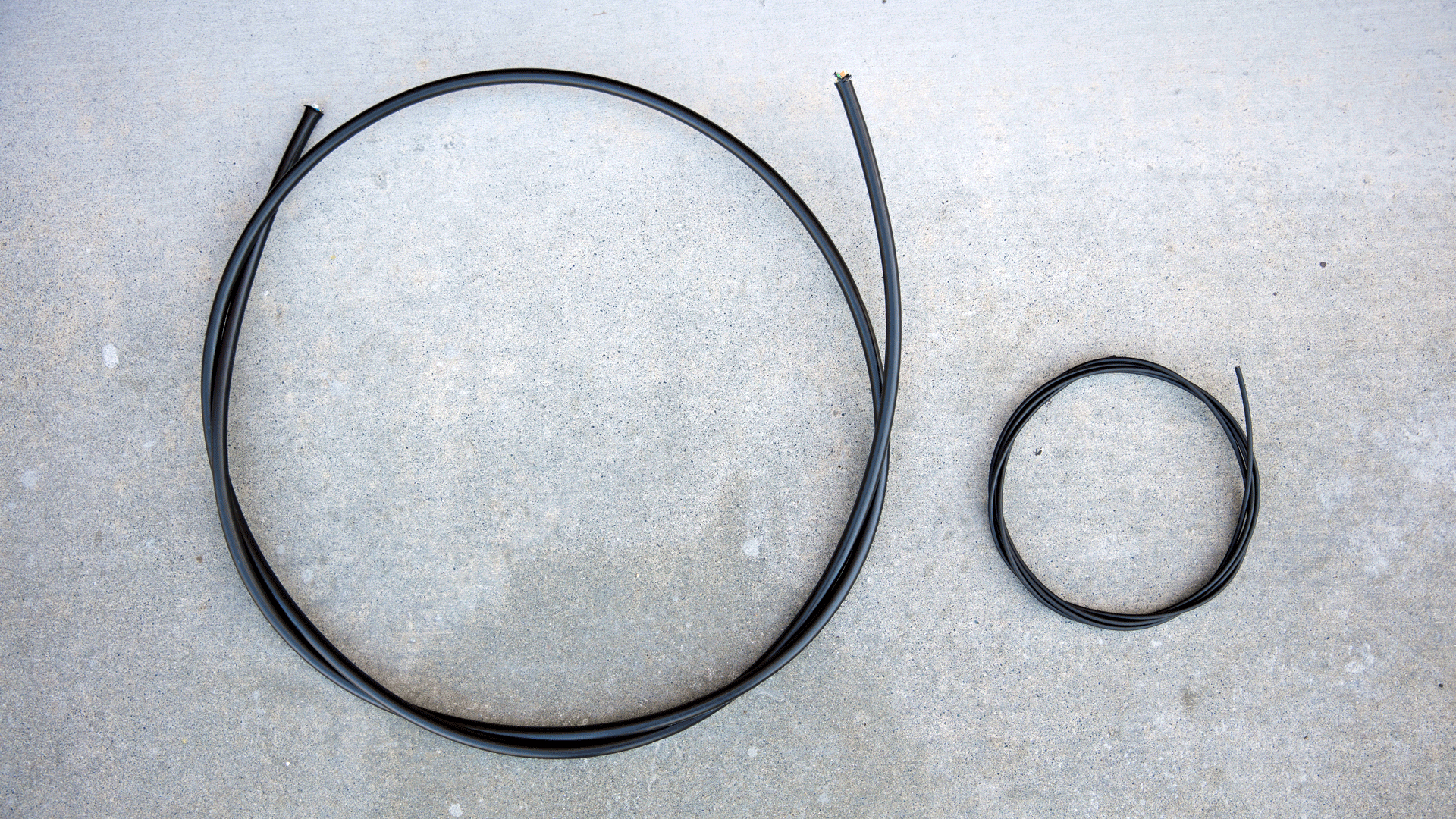
Even with a 4 mm OD cable, we still had problems, caused by the cable volume and counterweight. A traditional helical wrap solution uses a standard spool, which turns to pay off the cable as it is orbited around the conductor.
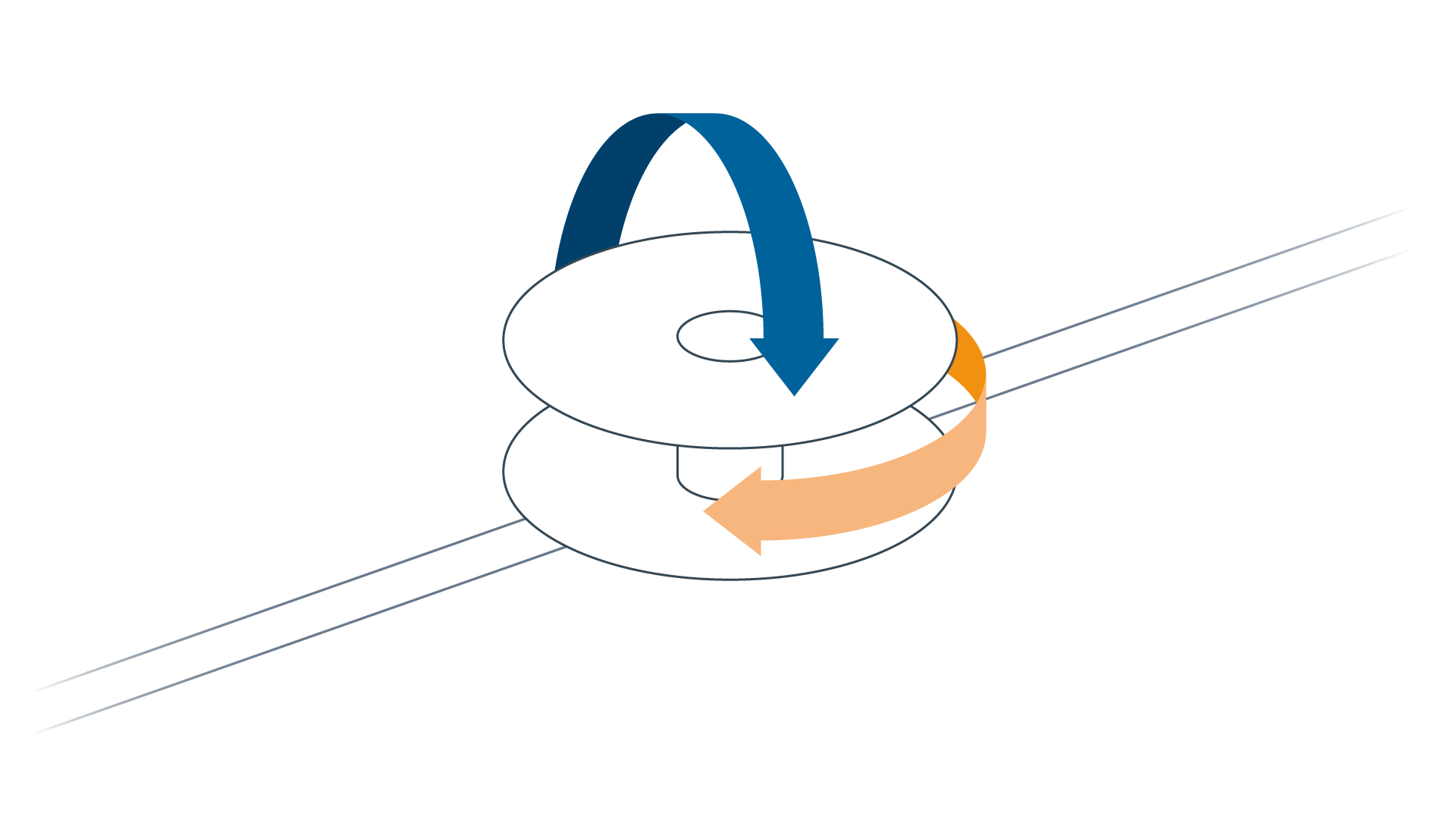
With a standard spool sitting offset from the conductor, the available clearance around the conductor would limit the maximum flange diameter and spool height. As a result, even with the reduced fiber diameter, a standard spool would be unable to carry the required amount of fiber. Furthermore, the offset spool center of gravity would require a counterweight, which in turn would restrict the weight budget of the wrapping machine.
Solving this problem took dozens of extremely varied approaches over a number of years ranging from spools with driven surfaces, curved, and even multi-axis mandrels. In the end, our solution was an upgrade of a technique first developed for military applications, which requires no spool at all. Instead, we created a spool-free cable coil geometry that meets all the clearance requirements around the conductor to allow passing obstacles, all while maintaining a center of mass aligned within 2 mm of the center of the power line, removing the need for both the weight of the spool and the counterweight.
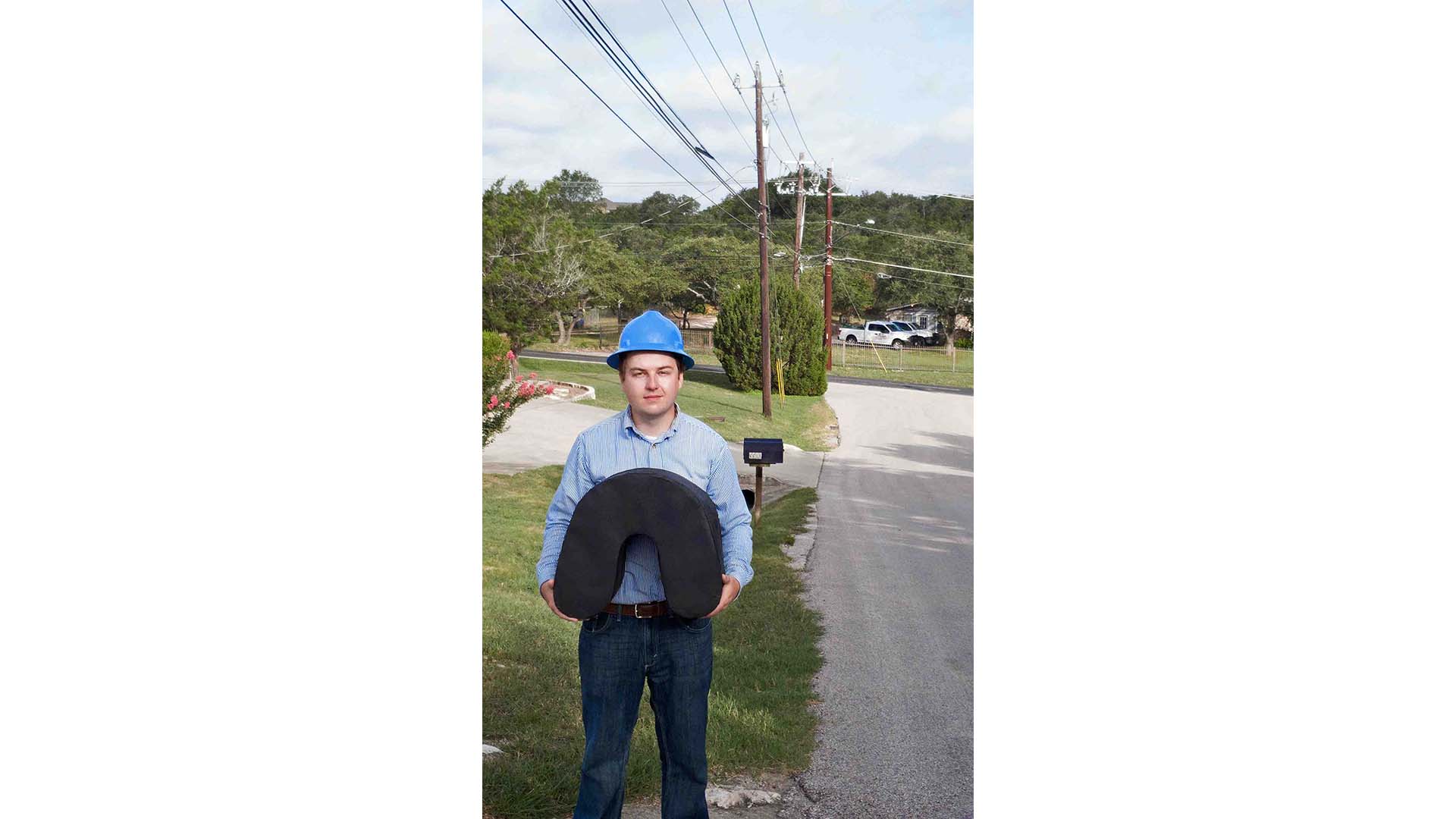
This brings us to the last big challenge, which is the wrapping machine itself. As mentioned earlier, MV conductors are most commonly deployed in a bare overhead configuration that relies on clearance around the uninsulated conductors to prevent arcing or fires. With thousands of electric utilities around the globe and over a hundred years of evolving standards, the number of permutations of support structures, insulators, taps, and other obstacles is vast. However, the requirements governing the design of the conductor supports have a common goal of preventing electrical hazards, so the clearances, approach angles, and loading limits required for safe navigation across these obstacles can be distilled to one common, albeit challenging, set of requirements.
First, our system needs to allow installation of fiber while the conductors are energized. This is necessary because extended outages would inconvenience the homes and businesses in the area. This requirement, in turn, made it necessary for the wrapping machine to be able to cross all the obstacles on its route without human assistance or intervention. To find a solution to this problem, we talked to a number of robotics companies across the globe. In the end, we selected ULC Robotics , based on their innovative concept design and their decade-plus of experience designing robots for high-reliability utility applications.
The resulting ULC design comprises a pair of drive subsystems, a lift subsystem, and a rotation subsystem. The robot's drive subsystem comprises a pair of driven grippers that can be moved relative to each other to accommodate obstacles and conductor angles. To pass an obstacle, the lift subsystem raises the payload and rotation subsystems from their normal cable wrapping position, which has a center of mass aligned with the power line, up to clear the obstacle. During this operation, the robot is put in an unbalanced state (like a tightrope walker) and uses a stabilizer to balance itself as it crosses the obstacle, after which the payload and rotation subsystem are lowered, and the wrapping operation continues.
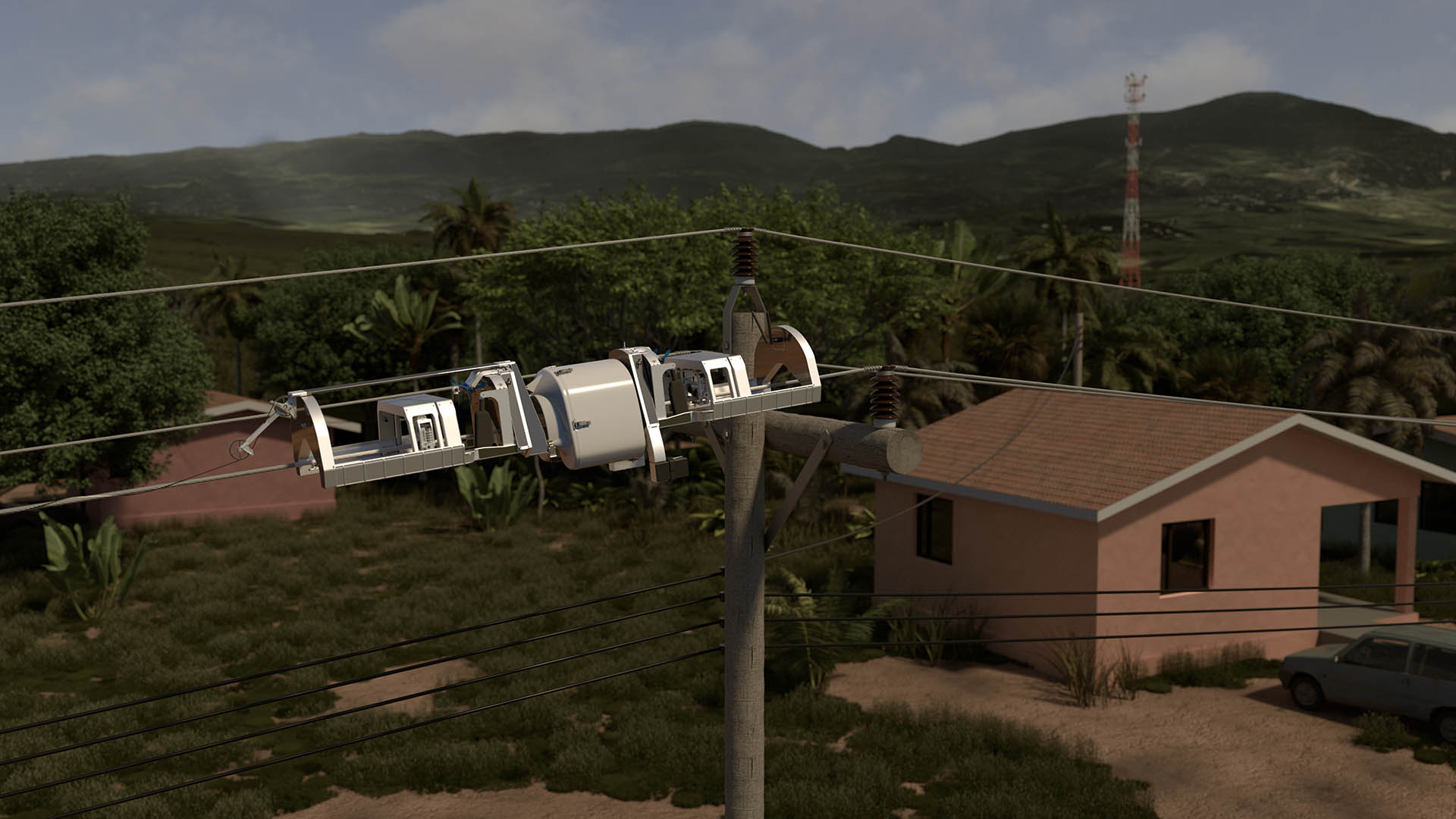
The robot also includes a vision system to identify obstacles and appropriately adjust its movements to clear the obstacles while maintaining the clearances required to prevent an electrical hazard. The shape and material properties of the robot are currently being optimized for weight and safe operation on live lines.
How it works
Each robot will be capable of installing over a kilometer of fiber and passing the dozens of intervening obstacles autonomously in approximately an hour and a half. To account for the human interaction steps such as setup, loading and unloading the robot, installing transitions, etc., we have been conservatively estimating an overall build speed of 1.5 km to 2 km per robot per day on average.
While traditional aerial fiber deployment involves heavy machinery, reel carts, large spools and large crew sizes, a fiber deployment crew deploying our solution, will comprise two or three electric utility linemen and a pickup truck with a few kilometer spools of fiber, a robot, and a few accessories, allowing many crews to work in parallel. These accessories will include an apparatus, developed by our partners Quanta Services , that's designed to allow the robot to be safely loaded and unloaded from the live line by the line staff. There is also a custom cable clamp, which can be used to periodically clamp the fiber to the power line using a hot stick, along with a specially designed splice case and phase to ground assembly. We expect the total cost, including labor, depreciation, and materials, to be between $2 and $3 USD per meter in developing countries.
By lowering the total cost of aerial fiber deployment, we expect that our system will have a significant impact on internet penetration, especially among the half of the world earning less than $5.50 USD per day. This is thanks to a subtle benefit of the enormous bandwidth of each fiber strand, which allows large capacity upgrades to be made via simple changes to the electronics on either end of the fiber. Illustrated in the chart below, with each small increase in cost, we get a large increase in capacity, resulting in the cost per bit falling over time. We believe this feature of fiber will help enable those even in lowest income brackets to be able to afford all the rich content the internet has to offer, helping to bridge the digital divide.
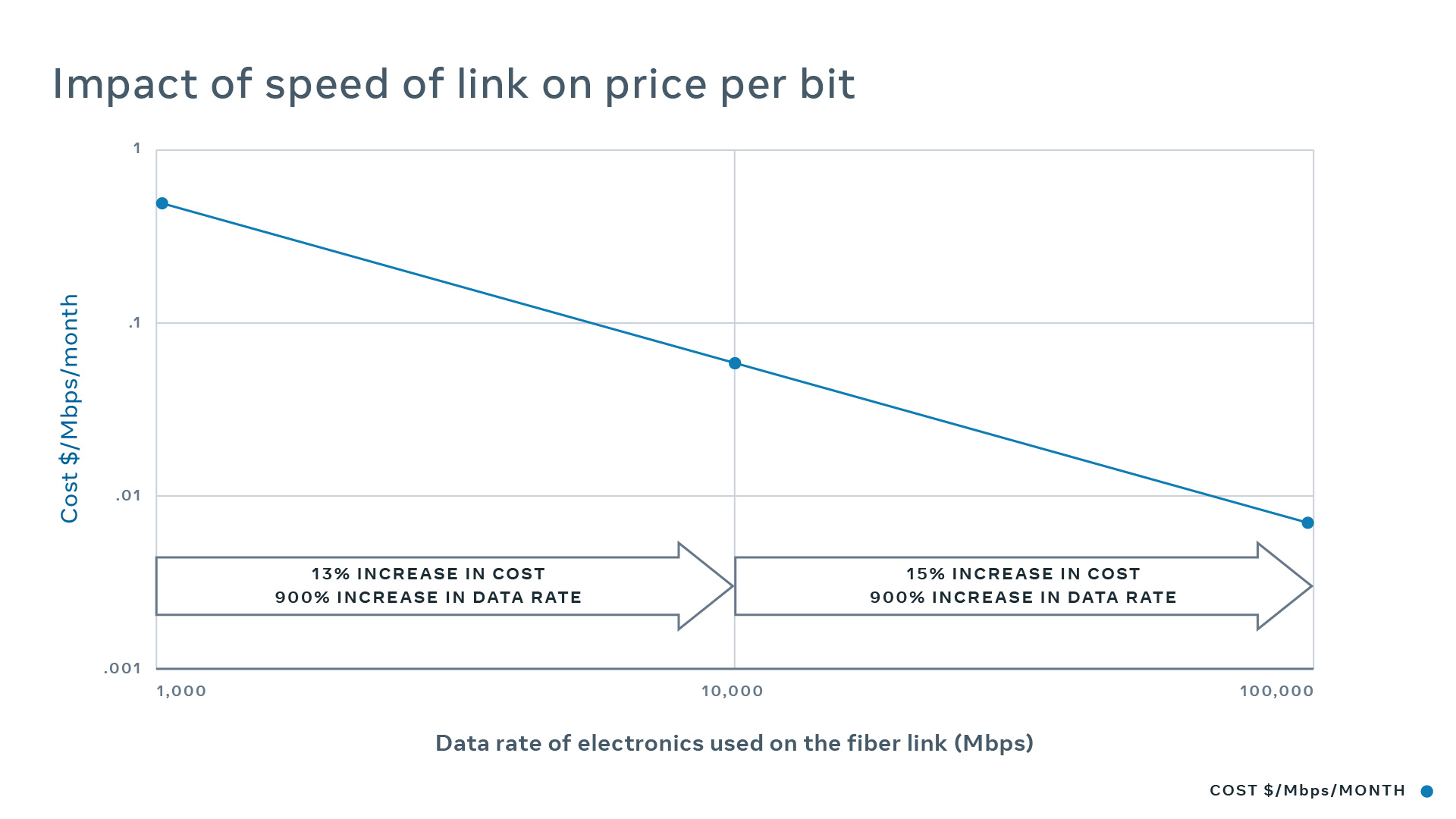
While we still have a number of steps to complete before our first deployment, we have confidence that this approach will yield a substantial improvement to both the cost and speed of fiber deployments. Achieving these improvements will require close cooperation with electric utilities. This technology relies on critical electric utility infrastructure, so its use is made possible only through collaboration with the local electric companies for both deployment and operations. We believe that fiber will also provide communication benefits to the electric utilities for their operations. We hope this technology will enable large-scale fiber deployments around the world and that the benefits of the abundant capacity will result in lower prices to the end consumer.
While there are too many people to mention, we would be remiss not to acknowledge the efforts and insights of Robert Olding, James Mass, Richard Ahlschlager and his team at Aurecon/Zutari South Africa, Greggory Bell and his team at Quanta Services, my colleague Carlos Vera, and the support of my manager and mentor Yael Maguire, without whom this project would not be where it is today.
Fiber Optic Communication Systems Agrawal Solution Manual Free Download Facebook
Source: https://engineering.fb.com/2020/07/13/connectivity/aerial-fiber-deployment/